Beginner’s guide to container conversions
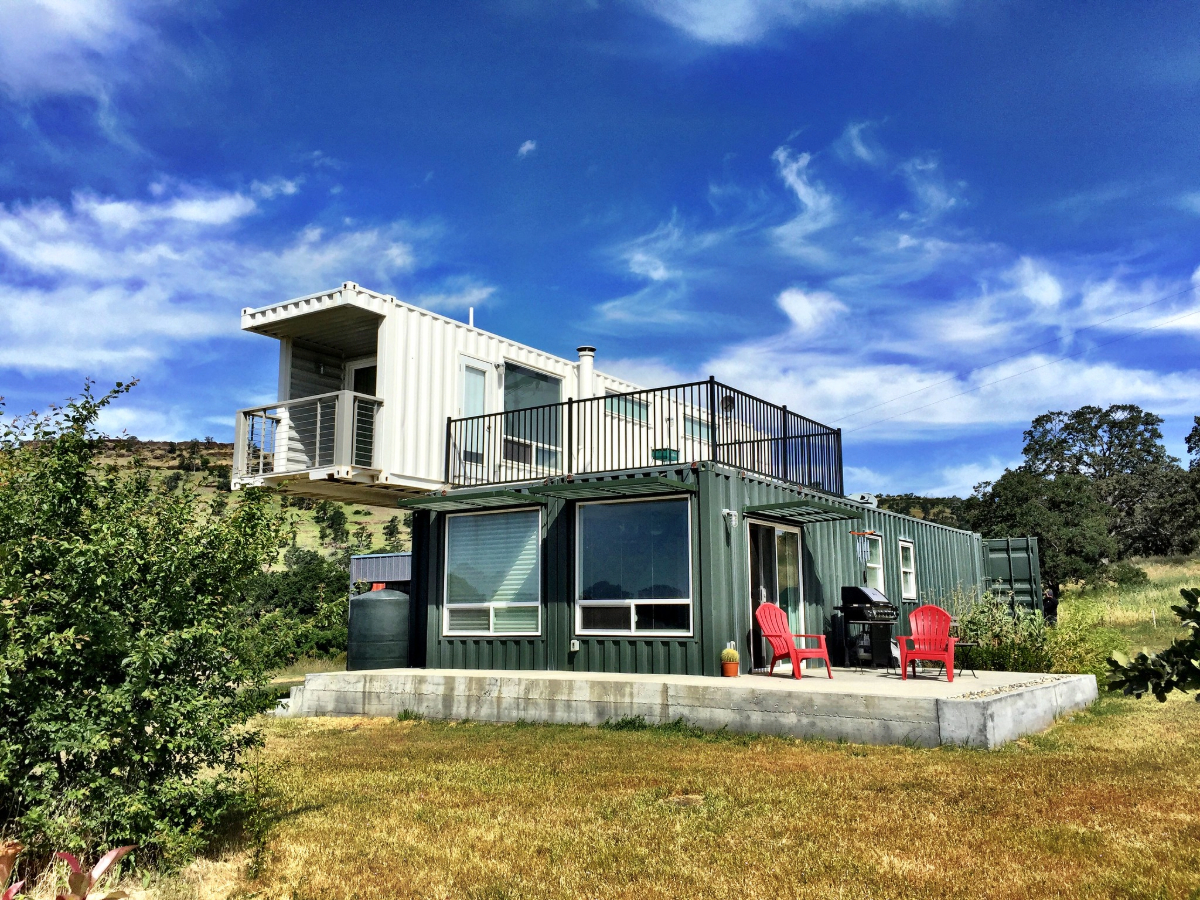
Last Updated on February 13, 2025
Containers are extremely versatile and can be converted for numerous purposes and in different layouts, from chemical stores, offices, canteens and workshops to exhibition units and even housing, with the correct guidance. This guide will take you through the process and provide you with inspiration for your own container conversion.
Where to start
It is vital to carefully plan for your specific purpose. You will need to consider what the container/s will be used for, and therefore what size container you need; whether a single unit will suffice or more than one needs to be joined together. The best way to start would be to draw an initial sketch layout, including windows, doors, and any interior partitions. Plan the placement of utilities, such as electrics, plumbing and any HVAC (air conditioning) systems you might require.
Shipping containers come in the following standard sizes: 10ft x 8ft, 20ft x 8ft and 40ft x 8ft. 45ft x 8ft containers are more rare but potentially available. Using new/one-trip containers is recommended as these will last a long time. However, second-hand container conversions are still possible as a cheaper option. Second-hand containers are not so aesthetically pleasing, with dents and surface rust, so this should be carefully considered.
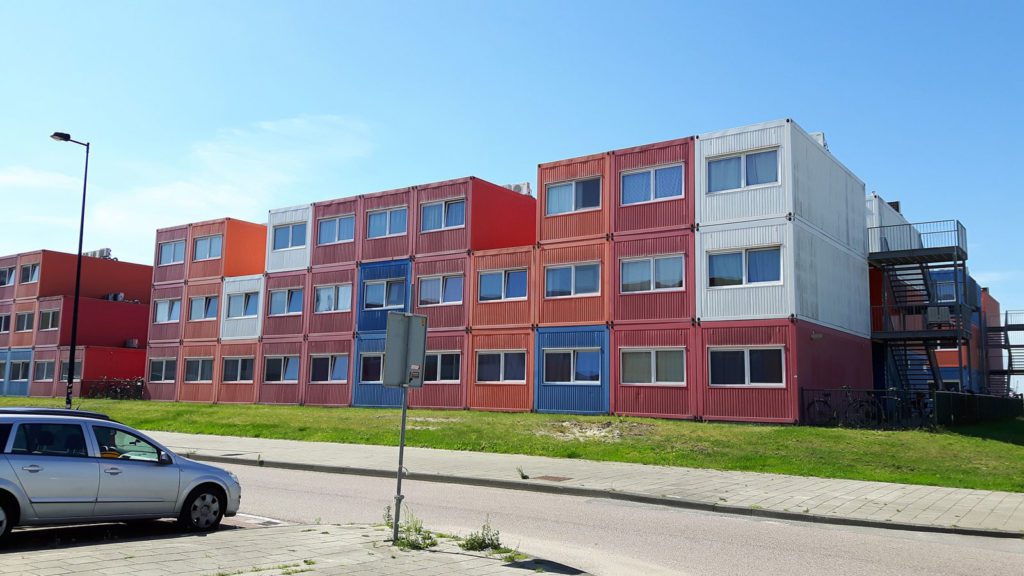
Combining multiple containers
It is possible to combine different-sized containers for a conversion; however, attention should be given to the height of the containers, as they will need to be all the same height to be easily connected. It may be best to opt for high cube height containers, which are 1ft taller than standard ones, as they offer more internal height once lining and insulation are added.
When connecting two containers of the same size, such as 10ft or 20ft units, along one long side, the wall can be removed from both containers without additional support. However, connecting 40ft units along the long side will require some form of roof support such as posts. The roof may also need to be reinforced using a sort of RSJ, similar to that used inside a house when a wall is removed. In this case, taller high cube units would be much more suitable, especially when joining 40ft/45ft containers – and particularly if there are more than two – as they will require additional roof support due to the length.
If containers are to be joined together, bear in mind that they cannot be transported to your site as one unit due to highway regulations. Connecting the containers on site would need to be factored into the project, by welding or bolting together. You may choose to handle this yourself, or we can assist you at an additional cost.
Can I live in a converted container?
Transforming a container into a home is possible; however, it is essential to seek guidance from a structural engineer, architect and the building regulations department of your local council. Specific materials must be used to ensure compliance with the regulations. The building regulations department will be able to advise on these. We recommend you contact your local council with your plans before starting any conversion work to confirm your proposals are approved.
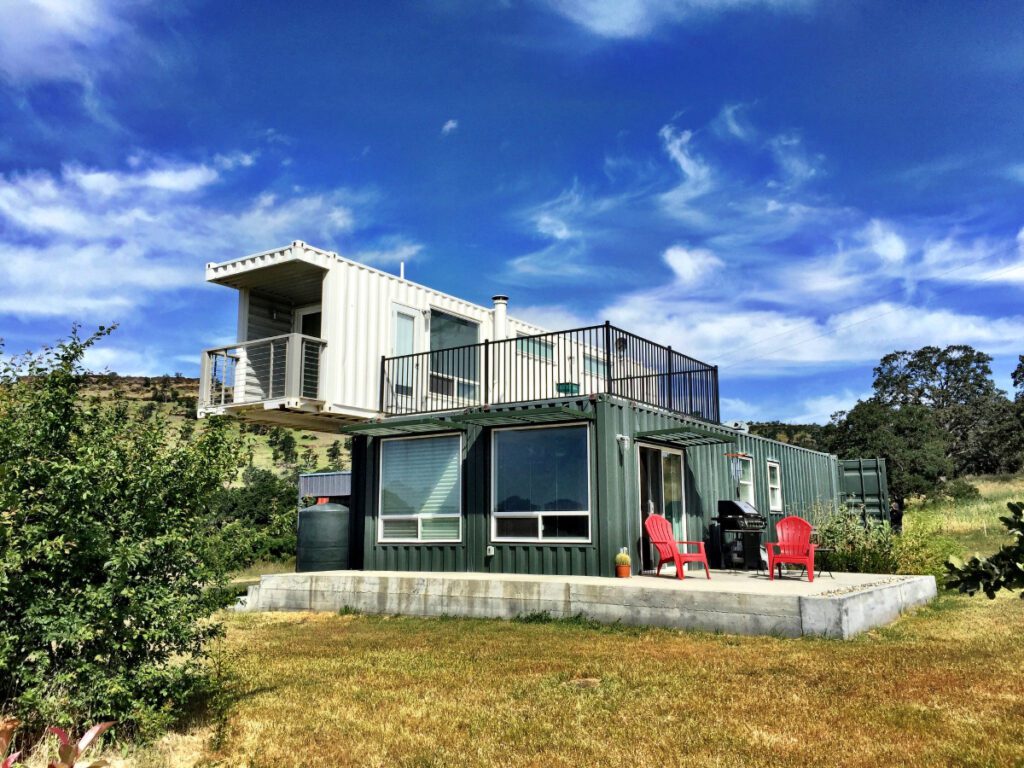
Solid ground
Containers must be sited on a firm, level base. If the container is not perfectly level, it could twist which would cause problems opening and closing the container doors. Single units can be sited on blocks, bricks or railway sleepers. For larger conversions of more than one container, a full concrete base would be the best option, as it can be made level and will be strong enough to support the weight of the converted containers.
Inspiration for your container conversion
Container conversions can involve adding windows, doors, lining, insulation, additional vents, partitions, external cladding, floor coverings, electrics and plumbing, as well as joining units and repainting.
Room with a view
Any openings cut into the container, such as windows and doors, will need to be edged/reinforced with a steel framework to help strengthen the area cut and prevent sharp edges. Insulation is vital to keep the container warm in the winter and cool in the summer, along with plenty of ventilation to prevent condensation.
Utilities
All electrical works should be done by a qualified and licensed electrician and must adhere to local building codes.
Plumbing should be planned and the water source identified. This may involve connecting to the mains on-site or using a water bowser that could be positioned under the container, provided the unit has the correct support to raise it sufficiently. Additionally, wastewater management should be considered, either via the main sewage system or a septic tank, which could potentially be located under or near the converted container.
Heating and air conditioning should also be considered as containers can become very hot in the summer and very cold in the winter.
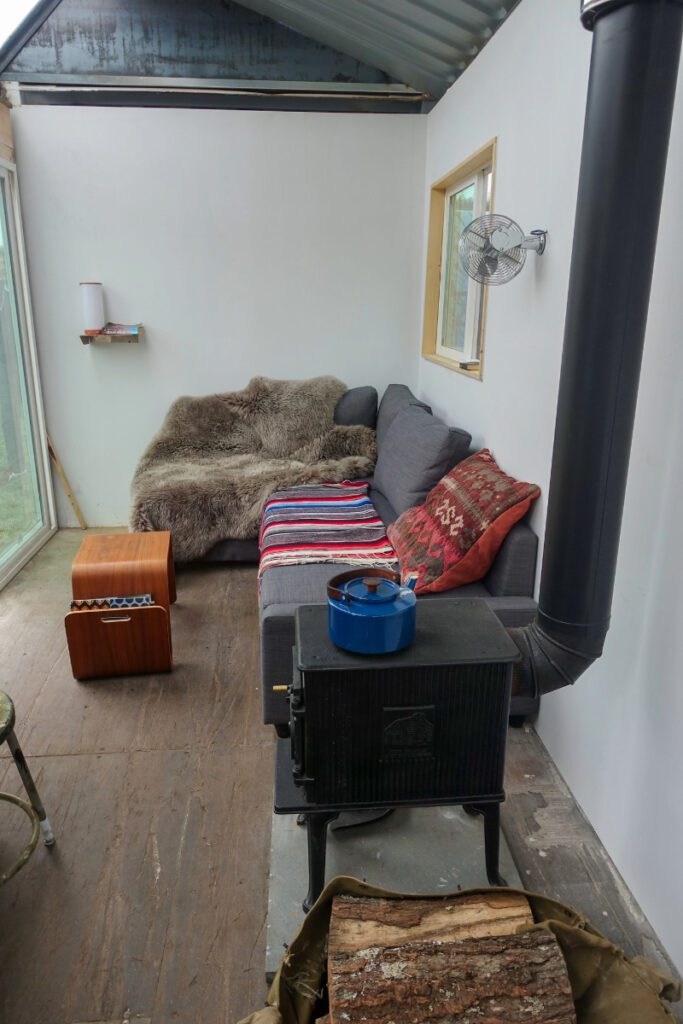
Interior decor
There is a variety of floor covering options available including vinyl, laminate, etc. It is possible to use tiles for the floor or walls; however, it is best to have these fitted on-site once the container is in its final resting place, as they can move or crack when the container conversion is lifted on and off the delivery vehicle. Walls can be lined with melamine, plywood or steel. Plasterboard is another option; however, this may also crack or split when the container is moved for delivery, so this should be carefully considered.
Storage and furniture
Kitchens can be fitted in converted containers, which work very well; however, any loose items such as sofas should be situated once the container is on-site and in position, to avoid breakages. Any items to be attached to the wall should be noted in the initial planning so that additional noggins can be fitted behind the lining boards for added support.
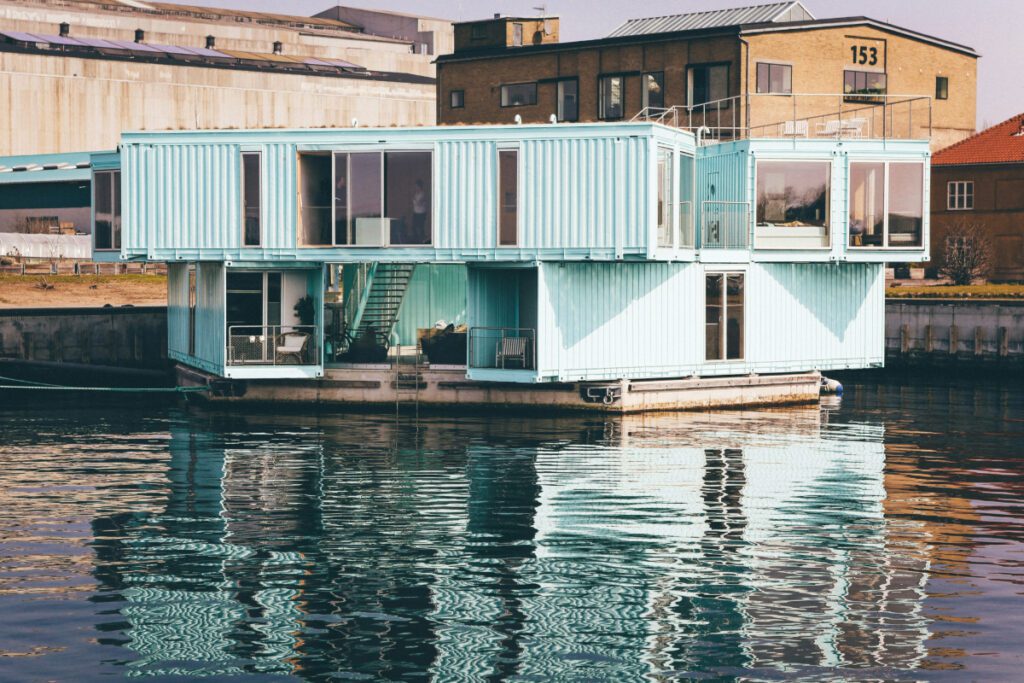
Final checks
Once the conversion has been completed, the works should be checked for any minor defects, and electrical testing carried out, before and after installation of the container.
Container conversions are an affordable solution and a great way to create a functional space. They provide a quick option with the advantage of being temporary structures, enabling relocation from one site to another if necessary. This makes them particularly cost-effective, especially for businesses.
Get a quote or telephone us on 0800 121 7388. We look forward to hearing from you and will happily answer any questions you have about converted containers.